Harvest B opened its first alterative protein manufacturing facility in Western Sydney on Tuesday, hoping to start a fundamental shift in Australia’s $85 billion agriculture sector. The venture is looking to disrupt the current approach of shipping produce offshore to be processed, only for it to be bought back at higher costs as finished consumer products.
The facility will produce around 1,000 metric tonnes of plant-based proteins and will do so using all Australian-grown grains.
The outputs will go to companies that make the increasingly popular “meat-free” sausages, patties, and mince, locking in for the first time an all-Australian plant-based protein value chain for the products.
The company, which has raised $4.5 million dollars and benefited from a range of government innovation programs, will also manufacture full pieces of protein in an entirely new way, promising an even cleaner and cheaper alternative protein.
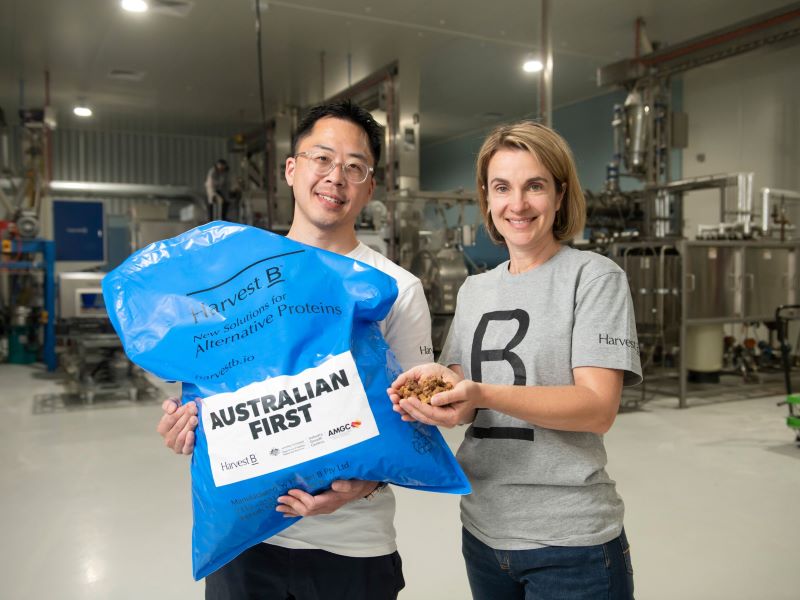
It’s exactly the sort of shift governments want to see: value add, specialist domestic manufacturing that lessens the nation’s environmental impact and reliance on global supply chains. All while creating new jobs and opening new export opportunities.
“As climate change impacts food supply chains, developing alternative proteins will emerge as a global challenge,” Industry minister Ed Husic said at the Harvest B opening.
“Harvest B can now supply plant-based proteins to food brands and manufacturers across Australia, establishing a new local supply chain and increasing Australia’s domestic manufacturing capability and export potential.”
Australia is the world’s third fastest-growing market for plant-based foods, with local consumer spending expected to reach $3 billion by 2030. The global demand for protein is expected to increase by 20 per cent between 2018 and 2025.
The CSIRO this year forecast a $13 billion market opportunity for Australia to grow and diversify its high-quality protein products from various different sources.
Harvest B was created by venture capitalists and tech company founders Kristi Riordan and Alfred Lo in 2020 to value-add in Australian agriculture through alternative protein.
The founders describe it as a “B2B plant-based meat wholesaler”. Harvest B supplies both the ingredients for established meat alternatives like burger patties or sausages and an entirely new plant-based protein created from its own IP.
Using Australian wheat and some imported soybeans, Harvest B can produce full pieces of protein it claims has a similar texture and taste to non-processed meat like chicken or beef.
The approach solves the “extreme problem” with plant-based meats of relying on long global supply chains to manufacture end products that too often are a “cute meat replacement” but not a genuine, sustainable alternative, according to co-founder Alfred Lo.
“It’s something that could substantially replace the protein mix for humanity. And that’s what we are working on at Harvest B,” said Mr Lo, who has run multiple venture funds and was chief investment officer at deep tech incubator Cicada Innovations before launching the manufacturing company.
Unlike the meat alternative sausages and patties now commonplace on supermarket shelves, Harvest B’s full piece protein is made with only two ingredients using the company’s process of denaturing proteins and realign them into more of a muscle like tissue to create a meat-like texture.
“Despite the fact that you might love a good burger, you’re probably not putting that on your plates at home or going out to restaurants and having that every day,” Harvest B co-founder and chief executive Kristi Riordan told InnovationAus.com.
“So, to really capture the market, we need to get people thinking at how they can include these proteins in their everyday meals.”
The Harvest B pilot facility in Penrith will produce both ingredients and the full protein products. It was opened by Industry minister Ed Husic on Tuesday.
“Harvest B’s high-quality, locally sourced products will boost Australia’s plant-based food industry, which has strong potential for future growth,” he said.
Ms Riordan says the new facility will scale up to its around 1,000 metric tonnes capacity by the end of next year and has commitments from both food manufacturing brands for ingredient supply and restaurants for the new proteins products.
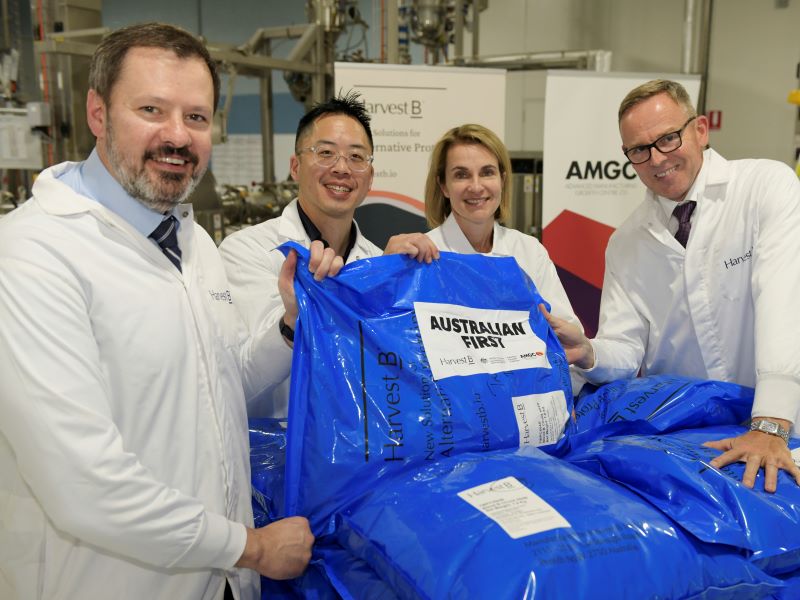
But the company is looking overseas for a much bigger market, targeting rising demand in Asia for plant-based protein and potentially lower costs for full scale production.
“We have to be able to deliver a product at a cost that the market will bear,” Ms Riordan said.
“So we don’t have sufficient market scale here in Australia to support infinite scale, we have to be able to export and do it cost effectively. And part of that is what is the environment in which we established manufacturing.”
It may take the federal government’s centrepiece industrial policy — the $15 billion National Reconstruction Fund — to keep Harvest B manufacturing onshore, with Ms Riordan saying the program could “tip the scales” towards Australian manufacturing at scale.
Accessing the fund — which has set aside $1 billion for advanced manufacturing and another $500 million for value-add in agriculture, forestry, fisheries, food, and fibre — would mark a full maturation through government innovation programs for Harvest B.
US-born Ms Riordan arrived in Australia as one of the first recipients of the Global Talent visa program, with Home Affairs officials connecting her with the Advanced Manufacturing Growth Centre (AMGC).
The government-funded growth centre provided support and a $1 million commercialisation grant, while private investors, including Woolworths’ venture arm, W23, have backed it to take total fundraising to $4.5 million.
AMGC’s support made private investors’ capital more efficient, added “credibility” to the manufacturing venture, and connected the founders with the wider industry, Ms Riordan said.
“The challenge in manufacturing is that it’s not where venture capital has been putting its money for the last 20 years. So it’s a real step change,” she told InnovationAus.com
“On the other hand, when you think about where many of the investable opportunities need to be from a systemic perspective over the next 20 years, it’s going to be infrastructure, lots and lots of different kinds of infrastructure.
“So government has a huge role to play in incentivising that. And not to do it alone, but to help create the right incentives such that the right private capital will come in and support it.”
AMGC managing director Dr Jens Goennemann said it is increasingly important for Australian manufacturers to operate in intermediate goods.
“75 per cent of global trade happens in intermediate goods. Only 25 happens in finished goods,” he told InnovationAus.com.
“For Australia to play in an intermediate, unfinished, good area and be globally competitive and deliver into global value chains is exactly the place where we would like to see Australian manufacturers. Better, not cheaper, globally competitive — competing on value, not competing on costs.”
That is the economic argument, but the climate crisis adds a new imperative to alternative protein.
“If we then look at climate change and global warming; it’s global, it’s not Australian warming.
“So if we want to do something, and have alternatives [for] how to eventually feed 11 billion people, I think we are well placed to have a value proposition out of Australia. [We can] somewhat disrupt ourselves in the traditional way of how we feed the chicken and a cow and butcher it, and have something different to that and decarbonise that way,” Dr Goennemann said.
Do you know more? Contact James Riley via Email.