A rapid-prototyping co-working facility in Melbourne has developed face shields for frontline medical workers amid emerging shortages in the health system, pivoting to full-blown manufacturing operation.
FAB9 founder and chief executive Hans Chang is re-purposing his factory to produce the face shields locally, amid disrupted global supply-chains and is working with doctors and nurses at Footscray Hospital to lock down the design.
His factory is known as a giant “makerspace”, housing cutting-edge, open-source digital tech like CNC Routers and 3D printers ready to be deployed for manufacturing. Fab9 is a manufacturing setcor coworking space used for rapid prototyping. But the business has pivoted in the wake of coronavirus outbreak and lock down.
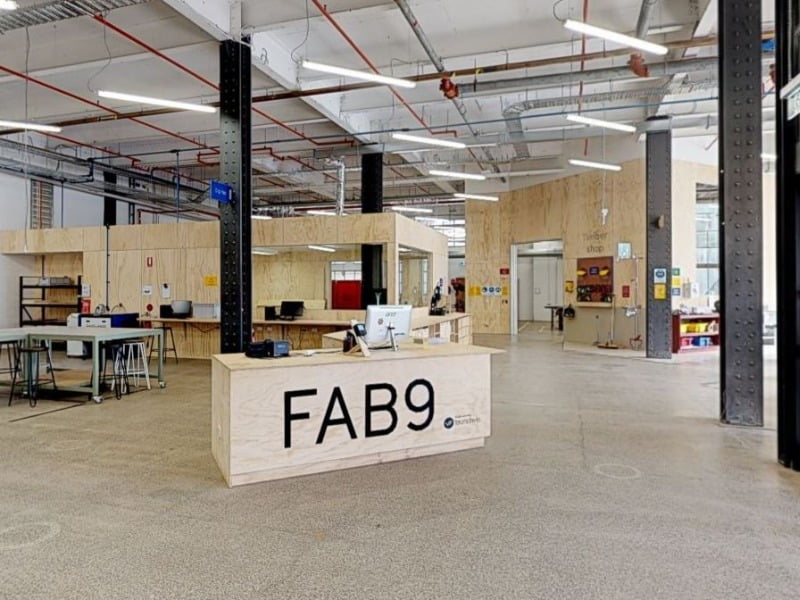
The operation will employ recently laid off workers to produce the face shields, which will then be sold to hospitals via the government health system.
“Makerspaces are a fusion of technology, activism, and civic participation and are fundamentally bottom-up, deeply engaging the local community for problem solving,” said Mr Chang, a former Silicon Valley executive.
“We would not have been able to conceive and launch a new PPE face shield product within a week if it weren’t for the different open source designs from other makers and companies.”
He has called for governments to work with the private sector to solve the PPE supply chain problem together and mobilise the private sector to produce PPEs and sanitisers locally.
“The NSW Premier has done so, other states, including Victoria should follow suit,” he said.
Mr Chang says the face-shield design is currently being evaluated by the hospitals and he expects to receive a purchase order imminently – with a goal to secure government contracts to manufacture in volumes of 100,000 to 500,000 units.
“To effectively combat the COVID-19 outbreak, speed trumps perfection, and to respond quickly we need to accelerate the cycles of learning and iteratively improve the solution,” he said.
He says local digital manufacturing startups are agile, innovative and community driven – helping ensure continued production amid the coronavirus shutdowns and economic downturn.
Do you know more? Contact James Riley via Email.