The Future Battery Industries Cooperative Research Centre has launched Australia’s first cathode precursor production pilot plant at Curtin University in Perth as the country develops new capabilities needed for a battery manufacturing industry.
At a value of $18 million, the plant features four fully integrated and automated precursor cathode active material (P-CAM) production units. The plant will build the capabilities needed to develop Australian P-CAM manufacturing facilities at a commercial and industrial scale.
Tests are to be undertaken over 18 months to trial the development of batteries with different compositions and ratios of chemistries, and varying production conditions such as temperature, pH, and stirring rate will also be tested.
With wide support from the mining industry, the project is being undertaken with 19 participants from research, industry, and government. This includes support from CSIRO.
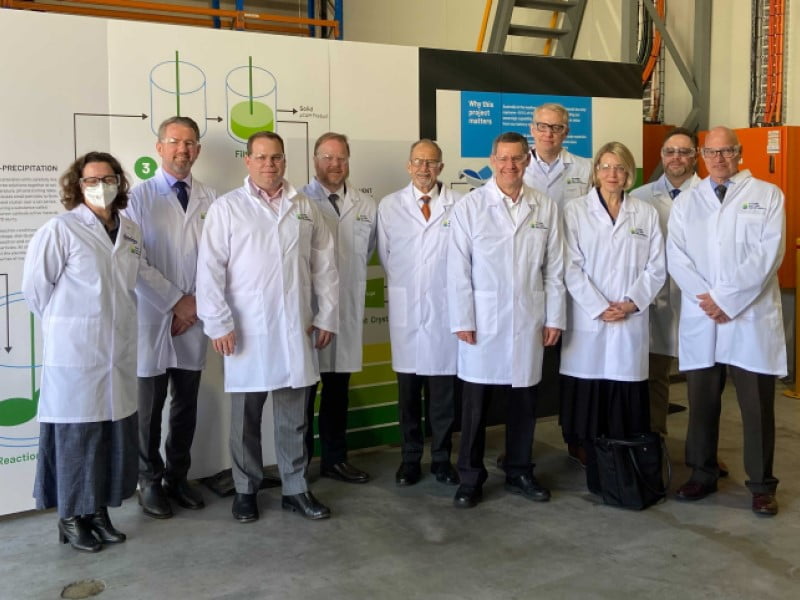
P-CAM must undergo further processing before they can be used in battery cells. For the Future Battery Industries Cooperative Research Centre (FBICRC) pilot plant, further processing and testing will be undertaken at the FBICRC-funded electrochemical testing facility at Queensland University of Technology (QUT).
FBICRC chief executive Shannon O’Rourke said that Western Australia provided a strong base for the development of a battery manufacturing industry.
“WA is already a leader in production for critical minerals, producing over 50 per cent of the world’s lithium supply, and is leading the way in mineral processing, taking those raw minerals and upgrading the value of them to produce refined chemicals like lithium hydroxide, manganese sulphate, nickel sulphate, and other chemicals,” Mr O’Rourke said.
He also added that with the Albanese government’s promise for a $1 billion value-adding in resources fund, $1 billion advanced manufacturing growth fund, and $3 billion powering Australia plan, the battery industry is “quite set up for success”.
“Australia has the potential to develop into a competitive player in the international batteries industry. The Pilot Plant launch is a significant step in developing the on-shore capabilities and industry knowledge to create thousands of jobs and add billions of dollars to our economy.”
Skills transfer from research to industry will be an important use for the pilot plant and will be used by universities and TAFE institutions to train chemical and process engineers.
Mr O’Rourke also added that building giga-scale battery manufacturing plants in Australia could happen much faster. He said that Australia should increase imports of existing P-CAM manufacturing technology in addition to local research and industry collaborations.
Australian battery materials manufacturing could be worth $1 billion by 2030 and support 4,800 jobs, according to the industry report commissioned by the FBICRC in 2021. Australia is already a massive producer of Nickel, Cobalt, Manganese, Graphite and Lithium, the essential raw materials for battery production.
Waste produced during P-CAM manufacturing will be used to make fertiliser, helping to reduce manufacturing costs and minimising the environmental impact of waste byproducts.
The P-CAM units have been provided by the Australian subsidiary of German chemicals manufacturing BASF. Other equipment was repurposed from BHP Nickel West’s Nickel Sulphate pilot plant.
BASF’s senior vice-president for global battery base metals and recycling Matthias Dohrn said told InnovationAus.com that bringing more of the battery supply chain to Australia would be beneficial.
“I believe in more local production, and if you look into value chains sustainability plays more and more of a role which consumers are more eager to have…When you ship raw materials, you actually ship a lot of material you don’t really want. Let’s say if that out of your ore the metal content is 30 per cent, you still ship 70 per cent of the material you don’t want to ship. This is all expensive and is not necessarily the right thing to do for the environment,” Mr Dohrn said.
Although Mr Dohrn believes that Australian exports of P-CAM “makes absolute sense” he said he has his doubts if it would make economic sense to export Australian-made electric vehicles.
The other key components of a battery cell are the anode, electrolyte, and separator. The FBICRC funds the QUT National Battery Testing Centre, battery materials research at the University of Technology Sydney, electrolyte research at Deakin University, and battery anode research at the University of Melbourne.
Curtin University also received $50 million through the federal government’s University Trailblazer program earlier this year to lead the Resources Technology and Critical Minerals hub.
Before being elected, the Albanese government committed to launching a National Battery Strategy The FBICRC’s 2021 report estimates that a national battery strategy could create up to 34,700 jobs and $7.4 billion in economic activity by 2030.
The Western Australian and Queensland state governments have already unveiled battery industry strategies.
Do you know more? Contact James Riley via Email.