Co-founders Tom Hussey and Brian Conolly teamed up in 2018 to transform the textile industry by addressing two of the sector’s biggest challenges: functional performance and sustainability.
Their vision was to create advanced materials that would not only provide functional benefits, with enhanced performance, comfort and protection, but also deliver sustainability benefits by reducing the environmental impact.
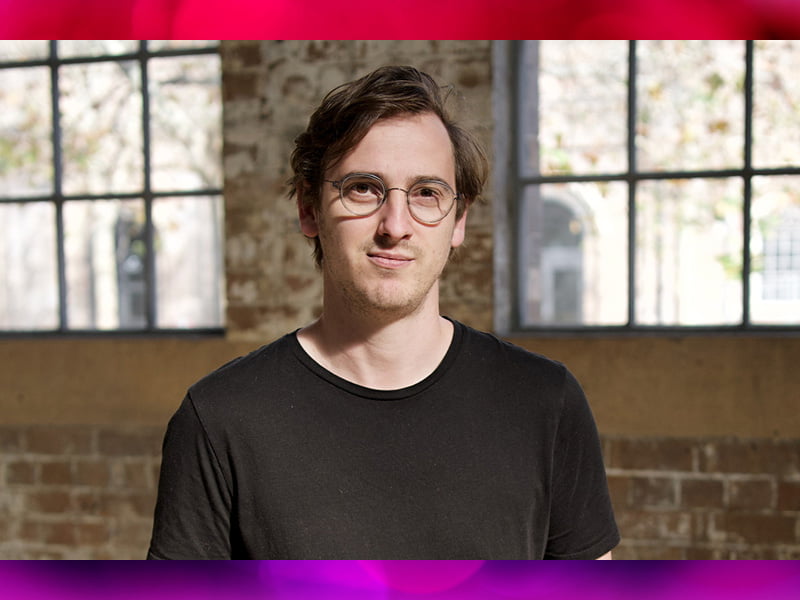
“We were trying to make a rash guard that never got wet,” Mr Hussey said, explaining they were working on new materials for performance apparel.
“When you’re in a surface water sport, as soon as your clothes get wet, the thermal properties of the clothing change significantly, and something that was warm, is now cold.”
Recognising the need for new thinking and new technologies, the inventive duo founded Sydney-based Xefco in 2018 to create new manufacturing processes to change the way the world makes fabrics.
Xefco has a growing global patent portfolio with over 34 patent filings across 17 patent families and has been named a finalist in the 2022 InnovationAus Awards for Excellence in the Manufacturing Innovation category.
The winners will be announced at a black-tie gala dinner to be held at The Cutaway venue at Barangaroo in Sydney. You can reserve your seat, or book a table, by clicking here.
The US$1.9 trillion textile market produces approximately 600 billion metres of fabric annually, Mr Hussey says, and is considered one of the world’s biggest polluters. He said traditional textile finishing and dyeing processes are destroying the world’s waterways.
“The existing processes and chemistry that was used to make things hydrophobic was pretty nasty from an environmental perspective, and also the performance was pretty poor, so it wasn’t actually possible to achieve the performance goals that we wanted,” Mr Hussey said.
Instead, the pair – which have 40 years combined experience leading R&D and innovative solutions in industry – set out to change things.
“We started looking at new processes that we could use to produce these textiles, these materials, that would give us a boost in functionality and allow us to use more chemistry – and that took us into industries and other fields of science to see what could be done.”
Fast forward to 2019, and Mr Hussey said the company commercialised its first technology, dubbed XReflex, which is an insulating textile technology that uses a novel atmospheric plasma coating system for sustainable manufacturing.
XReflex is now used by a number of leading global fashion and outdoor clothing brands including The North Face, Zara & Outdoor Research.
“Our core focus is the development and commercialisation of a sustainable dyeing and finishing technology called Ausora, which is intended to transform textile manufacturing by eliminating the extremely harmful wet dyeing and finishing process used throughout the industry,” Mr Hussey said.
“Our goal is to manufacture and export Ausora systems for use in textile manufacturing globally.”
Water-free process to transform textiles
The Ausora systems apply highly durable coatings to textiles via a completely water-free process of Plasma Enhanced Chemical Vapour Deposition (PECVD).
“Whilst this process is commonly used in the manufacture of semiconductors, touch panel displays and other advanced electronics, existing technologies and systems require a low pressure vacuum environment, which adds significant cost and creates other inefficiencies limiting the feasibility in textile production,” Mr Hussey said
“Our novel shower plasma processes enables the application of PECVD coatings at atmospheric pressure, eliminating the cost, inefficiencies and other limitations related to use of a vacuum chamber to deliver a highly efficient water-free manufacturing solution.”
The most exciting part, Mr Hussey said, is that Ausora systems will provide 100 per cent reduction in water consumption and wastewater discharge, up to 85 per cent reduction in chemical consumption, and 40 per cent energy savings in comparison to conventional textile finishing processes.
“By delivering a system that can apply PECVD coatings at atmospheric pressure, Ausora brings advanced thin-film materials science to low-cost, high volume applications.
“The technology has potential applications in a range of other industries including packaging, energy storage and generation, medical devices and more.”
The company plans to set up a pilot manufacturing facility in 2022 based in Geelong – located at Deakin University – to refine the technology at a large scale and facilitate commercial trials for customers.
Following the completion of the pilot, Xefco is targeting its first commercial systems to be operational at customer textile mills by the end of 2023.
“We intend to commercialise our Ausora systems via a pay-per-use service model to enable easy integration into textile manufacturing supply chains.”
Do you know more? Contact James Riley via Email.