Australia’s long-standing “dig and ship” resources mentality is changing quickly, driven by trading partners’ environmental and geopolitical concerns. One of the local companies in the race has warned the federal government needs to offer more strategic support to the budding local sector, and do it quickly.
Pure Battery Technologies (PBT), a University of Queensland spin-out that developed a greener, cheaper process for refining critical battery materials, is receiving interest around the world but wants to set up major refinement facilities in Australia.
Chief executive Bjorn Zikarsky said Australian governments needs to build out the local value chains more “aggressively” and strategically to keep them competitive in the global race.
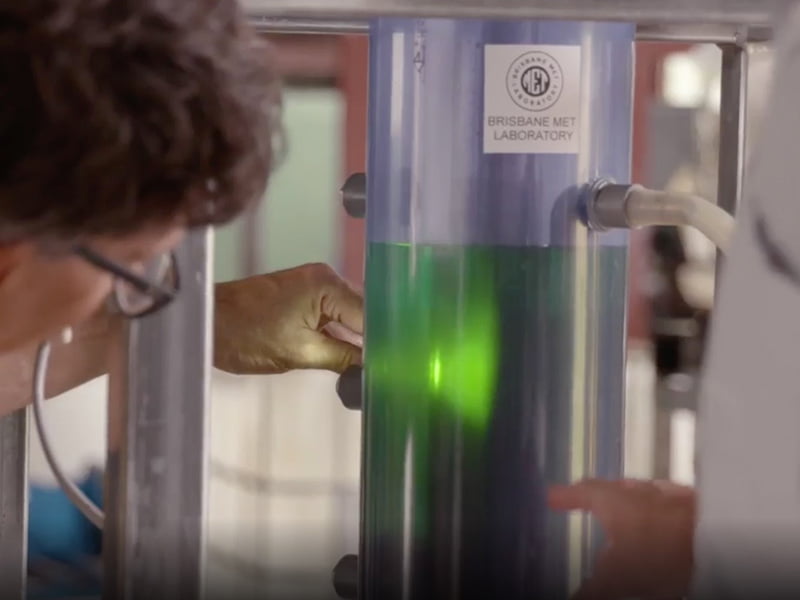
“In Australia, there is a dig and ship mentality where processing is done somewhere else. [But] that’s changing quickly because of environmental concerns about scope 1,2,3 emissions,” Mr Zikarsky told InnovationAus.
“So, more and more people are looking into how they can refine it and value add transformation of the metals at site.”
Australia and Chile dominate the resources market for critical minerals used in battery production, but almost all the refinement is done overseas, usually in China.
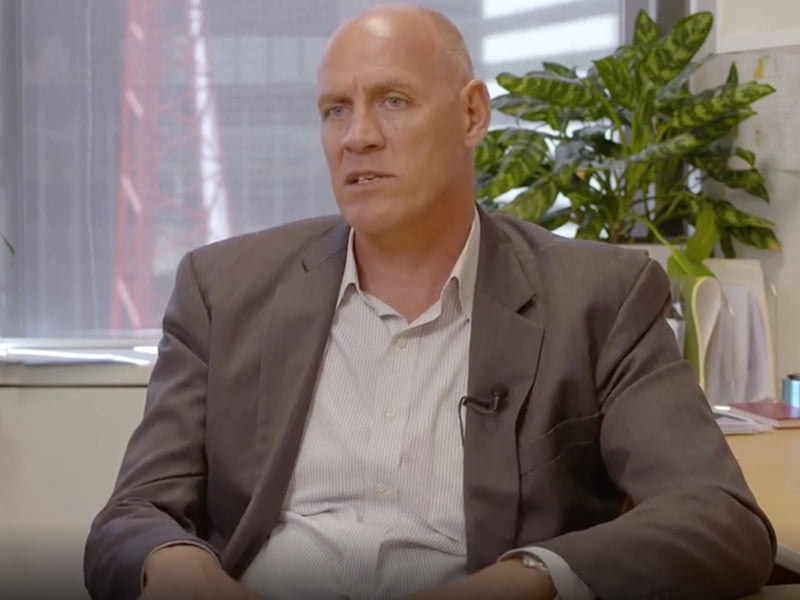
As the EU and US look for more sustainable suppliers, the value chains are changing, with governments around the world looking to capitalise.
In Australia, it is estimated an additional 7.4 billion and 34,000 jobs could be added to the economy by 2030 with a more diversified approach to battery value chains. Some experts have also warned being too reliant on China for critical mineral refinement and production creates geopolitical risks.
Mr Zikarsky said the federal government needs to move quickly to compete with other nations looking to onshore critical minerals industries or it risks losing its own and many innovative companies like PBT.
“We’re talking to the Department of Energy in the US, and just that department has a bucket for battery development of 44 billion US dollars. It’s not that they’re giving it away — there are some grants and some conditions — but they are aggressively trying to build the supply chain,” he said.
“The government in Australia needs to demonstrate that they’re on board to aggressively build that supply chain so these battery metals and materials for batteries can be exported for our trading partners.”
This year, the federal government opened funding for resources technology and critical minerals processing manufacturing projects under a dedicated stream from its $1.3 billion Modern Manufacturing Initiative, while another collaborative stream offers even bigger grants for large scale projects.
Earlier this week, the Prime Minister also announced a new $2 billion loan facility for critical mineral export companies.
But in the global race for a booming batteries market, governments need to do more than grants and loans, according to Mr Zikarsky, who would like to see the government take advantage of high demand to make international buyers contribute more to the local ecosystem.
“Have them pay not just for the material they’re getting yet also incentivise them to help establish the ecosystem that is developing our supply chain here in Australia, so it is competitive and stays here,” he said.
PBT’s own path demonstrates how even world leading technology still needs an ecosystem to thrive.
Established in 2017 to commercialise technology developed by The University of Queensland, PBT has developed a process to extract and process nickel and cobalt as clean energy material for use in lithium-ion batteries.
The process has the potential to drastically reduce the carbon footprint and manufacturing costs of electric vehicles.
The spin-out was able to access millions in early funding, including a $1 million federal Accelerating Commercialisation grant and a $2.2 million Cooperative Research Centres Project grant.
The government support was very welcome and was worth more than the dollar value of the grants to PBT.
The PBT chief said the Accelerating Commercialisation grant sends a signal to others and validates the work done to that point. The grant also requires a well developed roadmap for how PBT will commercialise its technology, something that has stuck years later.
“It creates a DNA in a company [that] carries you through. I think that is the one that helped us to get the technology into the next step, that helped us commercialise it.”
By 2019, PBT was closing in on a plan to build a 25,000-tonne refinery in Townsville. But the pandemic made financing a local facility difficult, and the company instead opted for an intermediate step.
PBT acquired a German refinery with around one-tenth the capacity to demonstrate the commercial viability of the technology to investors at a smaller scale. While it also helped to establish a European presence, Germany was as much about the speed and cost of establishing the new plant.
Licences to refine nickel are not issued lightly, typically taking several years for final approval. But buying an existing refinery is much faster.
“We tried to do it here in Australia [but] we couldn’t find anything where we could take our technology and demonstrate it,” said Mr Zikarsky.
“It was a whole lot cheaper and faster to purchase the refinery in Germany.”
The smaller refinery is designed to show investors the potential for the original plan of a full-scale plant in Townsville, which is still on the cards following a fast-tracked feasibility study and negotiations with feedstock providers.
Western Australia has also emerged as an option for an even larger facility, and the company has environmental preapprovals and state government interest for both sites.
PBT is now in discussions with the Australian Government about supporting its first major plant in Western Australia, but Mr Zikarsky said the company can still not rule out another move offshore.
Do you know more? Contact James Riley via Email.