Half a billion dollars worth of federal government battery production incentives should target active material and cell manufacturing for new chemistries as well as advanced lithium batteries, according to industry stakeholders, who warn competing elsewhere could be unrealistic.
The $523 million Battery Breakthrough initiative, announced in the 2024-25 federal budget, will target “the highest value opportunities in the supply chain”, but specifics are yet to be designed.
A National Battery Strategy released in the wake of the Budget highlights active material production as a huge export opportunity and the need to diversify access to new battery chemistries. But the plan is “technology agnostic”, leaving room for debate on where the government support should go.
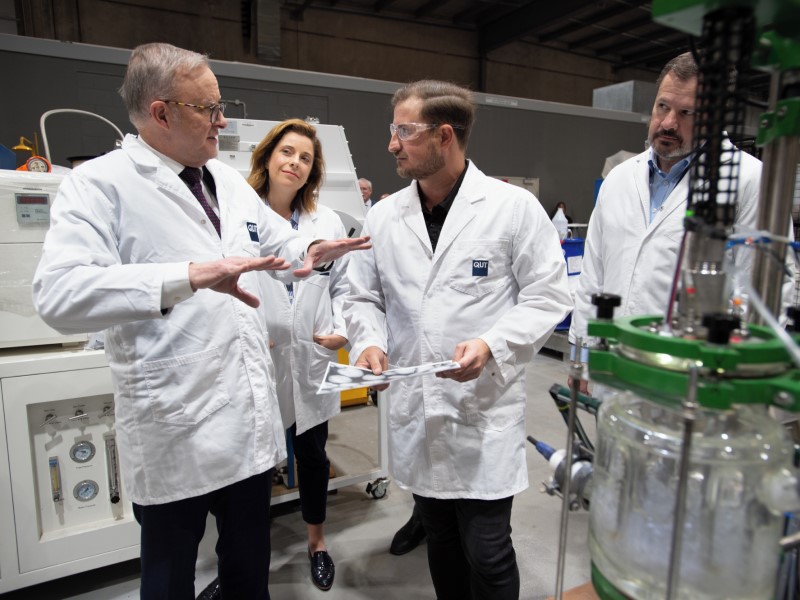
Speaking to InnovationAus.com about industry opportunities in the days before the release of the national strategy last month, industry stakeholders and experts were bullish on the need to support active material production for global EV supply chains.
But they shot down ambitions around EV cell or pack manufacturing.
While active materials production requires only one or two additional steps from the processing of critical minerals, cell manufacturing is the final step before the assembly of the final battery pack.
There is also a call for more research and development support for new battery chemistries, but some stakeholders stressed that there are emerging lithium-ion chemistries that can and should be produced now.
The Albanese government has already funded a $14 million battery industry growth centre, $5.6 million worth of due diligence for its promised Australian Made Battery Precinct, and $5.4 million in the 2023-24 mid-year economic forecast for a battery supply chain and research working group to partner with the United States government.
But the $523 million Battery Breakthrough initiative that will provide production incentives to industry looms as the big bet.
Experts say it should be aimed at active materials, battery cell manufacturing, and in developing batteries that are suited to the challenging climate
Queensland University of Technology’s principal research fellow in battery systems Associate Professor Josh Watts says there is a need to be “very strategic” about which downstream processing and manufacturing gets prioritised, urging the government to undertake more techno-economic analysis to get the detail on the greatest value opportunities across the value chain.
He is leading work on QUEST Hub, a Queensland government-funded facility aimed at deepening research and industry collaboration for developing and commercialising new battery technologies and materials.
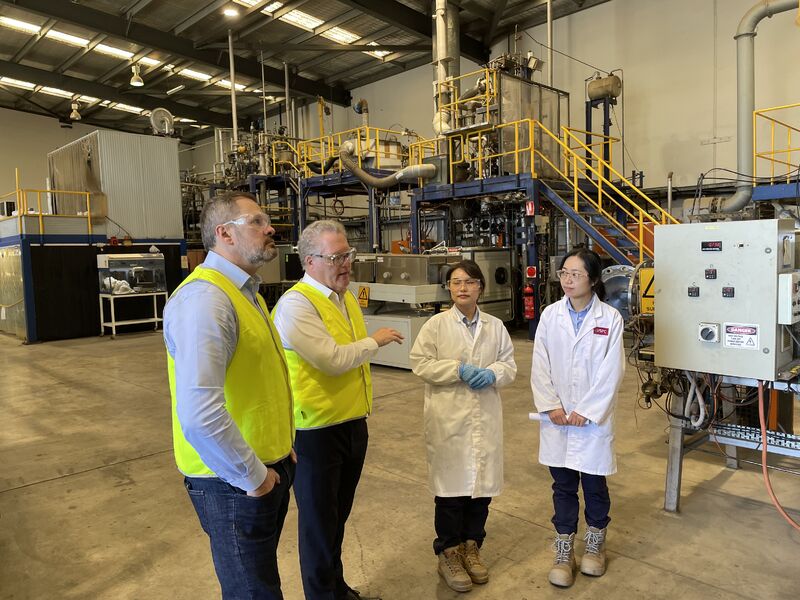
Battery chemistry innovation is something Australia can’t afford not to do, he says. But amid a global race to the bottom on the cost of producing existing technologies, “we can’t just carbon copy what everyone else is doing”.
According to Professor Watts, new chemistries could take five to 10 years to reach commercial scale and Australia must not overlook the immediate opportunities in advanced lithium-ion chemistries which have a shorter timeline to commercialisation and align with existing advantages.
In particular, he believes production incentives should flow to active material and cell manufacturing of advanced lithium-ion chemistries, for use in Australian mining, public transport, and defence electrification.
“We’ve got to focus in on what we have local demand for…[For example] we do make buses in Australia, so we can vertically integrate the cell supply with the manufacturers”.
Lithium Australia chief executive Simon Linge, whose ASX-listed company focuses on production of lithium-ion cathode active materials, said “we need to recognise we won’t be a battery pack production powerhouse”.
He told InnovationAus.com that Australia will likely struggle to bring the cost down for things like EV battery cell and pack manufacturing since it does not have vertical integration with automotive manufacturing like in China, South Korea, Japan and the US.
Instead, value chain opportunities will arise for battery technologies well suited to “hot environments and humid environments, where battery performance often deteriorates”. Mr Linge also agrees there are huge export opportunities for the production of lithium-ion cathode active materials.
Treasury analysis, released alongside the federal budget already flagged fierce competition among clean manufacturing incentives available in the United States, Europe, France, Canada, and India. Public and private cooperation on battery areas “relevant to Australia’s unique conditions and comparative strengths” will be needed, it says.
“It is likely these subsidies will lead to lower geographic concentration for specific technology in the future, and Australian consumers will benefit from any improvement in supply chain diversity and competition, subsidised by international taxpayers,” the report reads.
University of Queensland Centre for Policy Futures researcher and Advanced Materials and Battery Council (AMBC) director Dr Lynette Molyneaux similarly highlights the need to support the next generation of batteries that are yet to reach commercial scale, like aluminium-ion, lithium-sulphur, or stationary long-duration storage vanadium flow or iron flow batteries.
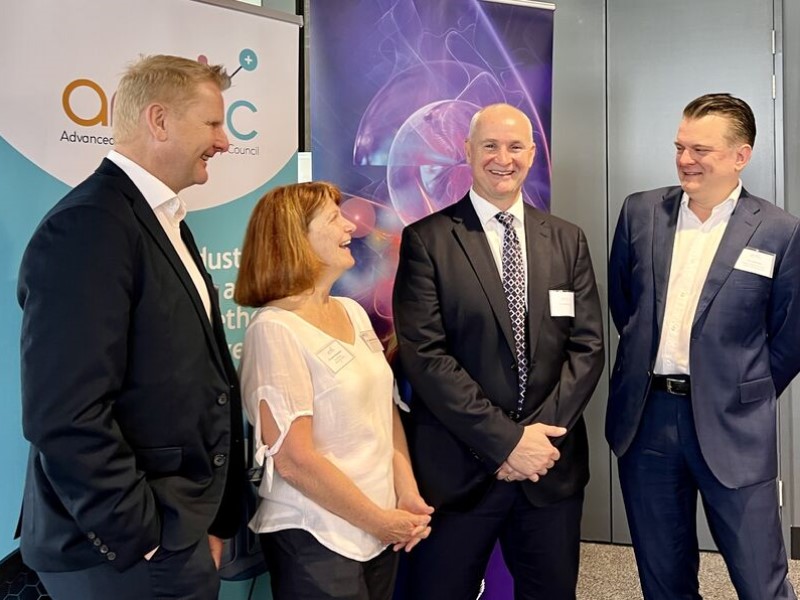
The AMBC is an industry representative group based in Brisbane that represents more than 20 battery industry companies across the value chain, and received initial seed funding from the Queensland government. The group also backs opportunities for cell manufacturing and active materials.
Dr Molyneaux explained that aluminium-ion and lithium-sulphur batteries have higher energy density, which means they could be light enough to support electrification of air and rail transport. Flow batteries meanwhile promise improved storage capabilities and safety.
AMBC chief executive Quentin Hill adds that some early value chain processing, namely for high purity aluminium as well as aluminium and vanadium pentoxide are ready now.
“Recent debt funding of these projects shows they’re ready to go and so money for that has the potential to boost them quickly,” he said.
“The cathode and anode active materials supplied will take a little bit longer, but this funding is required, and so in those sorts of things, we think [Battery Breakthrough will be] well targeted.”
Future Battery Industry Cooperative Research Centre’s (FBICRC) is home to a first-of-its-kind pre-cathode active material pilot plant and is currently in talks with the state and federal government to convert the pilot plant into a larger Critical Minerals Advanced Processing Common-User Facility. The FBICRC is also administering the federal government’s Powering Australia Industry Growth Centre.
Its chief executive Shannon O’Rourke highlighted that “mining, refining and advanced materials would contribute around $40 billion of the total $55 billion in GDP from the battery industry by 2030”.
These areas are where Australia has very strong competitive advantages”, Mr O’Rourke said. But an “integrated business ecosystem is a more effective and more sustainable approach to industry development”, rather than putting the spotlight on a highest value opportunity.
“Australia has an emerging downstream manufacturing sector which will benefit from thinking of the system as a whole,” Mr O’Rourke said.
Do you know more? Contact James Riley via Email.