The latest $3.6 million round of defence industry grants has been split between 10 local firms, with South Australia-based firms receiving the largest collective amount.
The largest individual grant in this round, worth just under $810,000, was awarded to New South Wales-based Armor Australia for the “construction of high-compression moulding stations”, to be used in the manufacture of armour for Defence personnel.
The funding comes through the Defence Global Competitiveness program and the Sovereign Industrial Capability Priority program, which both require grants to be matched by the firms.
The Defence Global Competitiveness program awards grants of up to $150,000, while the Sovereign Industrial Capability Priority program awards grants of up to $1 million.
The programs are open for applications on an ongoing basis, with the previous $3.8 million round announced in September.
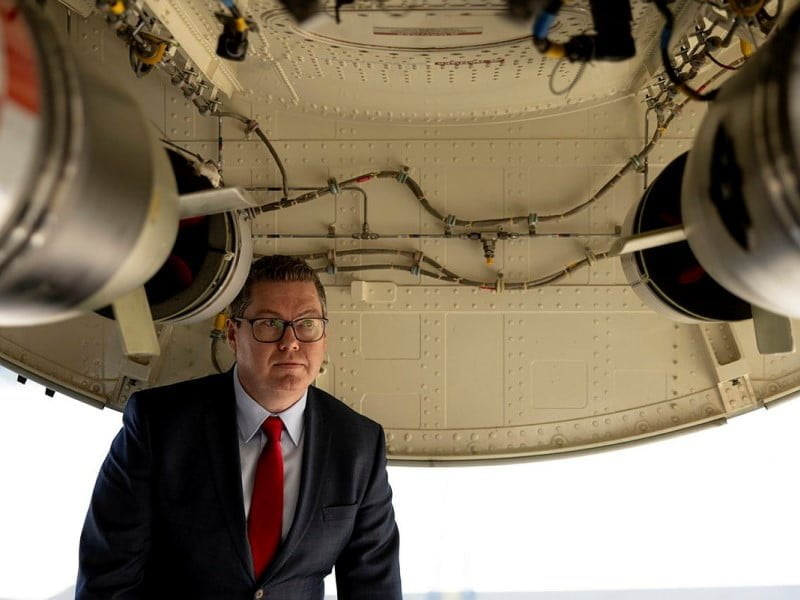
Department of Defence first assistant secretary for Australian industry capability Francesca Rush said the two grant programs continue to support “world-class manufacturing, both for Australia’s defence needs and for export”.
“The programs bolster Australian companies’ ability to continue to push the boundaries in developing cutting-edge capabilities, keeping our nation at the forefront of technological advancements,” Ms Rush said.
“They are essential to enabling our defence industry to grow, creating more jobs and opportunities for hardworking Australians, and contributing significantly to our national economy.”
Four firms from South Australia — Cold Logic, MyModular, Kennewell, and McMahon Metal Fabrication — shared more than $1.5 million.
Cold Logic received more than $585,000 for the installation of a “large-scale environmental test chamber facility for the evaluation of components and systems used in maritime, combat vehicles, and aerospace platforms”.
The firm specialise in the production of refrigeration solutions, with its defence division launching in 2018 after it won a contract with government-owned submarine maintainer ASC. It is currently delivering upgrades to cooling equipment for the Collins Class submarines.
Advanced Navigation has received $150,000 for the installation of a “calibration and testing system for validated production of sonar hydrophone sensors deployed in autonomous underwater vehicles”. The Sydney-based firm’s fibre optic gyroscopes enable highly accurate positioning and track useful for both defence and commercial applications.
This builds on its more than $830,000 defence industry grant earlier this year for the development of a custom fibre optic coil winding system for use in a gyroscopic inertial navigation system.
Victoria-based Advanced Composite Structures has received just more than $187,000 to purchase cutting, winding and geometric verification equipment to enable its manufacture of ultra-high-temperature fibre composite materials for use on hypersonic systems and space vehicles. The firm has worked in advance composites for more than 25 years.
The remaining grants were made to:
- Protonautics (Queensland): $150,000 for a computerised numerical control machining capability to produce components for the Boeing MQ-28 Ghost Bat and the Currawong battlespace communications system
- MyModular (SA): $420,166 to install specialised injection-moulding equipment to produce low-voltage lighting solutions used in shipbuilding facilities
- Kennewell (SA): $357,091 to acquire a coordinate measuring machine and video measuring system to form a metrology lab for geometric validation of complex manufactured components used in Defence maritime, land, radar and medical technology applications
- McMahon Metal Fabrication (SA): $150,000 to acquire a precision sheet and tube cutting metal fibre laser to fabricate metal components with technical capability and scale required by the US Navy
- Parish Engineering Company (Victoria): $291,334 to acquire a computerised numerical control lathe with barfeeder to produce air brake fittings and couplings for Defence vehicles
- IKAD Engineering (WA): $560,410 to acquire a range of computerised numerical control capabilities including wire cutter, lathes, turning and machining centres to produce complex components for naval ships systems
Do you know more? Contact James Riley via Email.